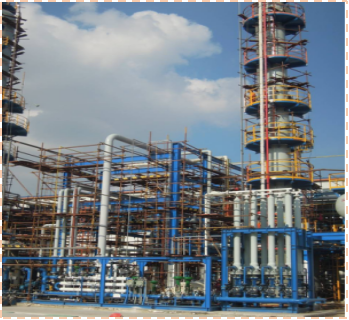
煉廠瓦斯輕烴及氫氣綜合回收
煉廠對氫氣的(of)需求,随着加氫工藝的(of)廣泛應用(use)及産品質量升級而迅速增加。優質、穩定、高純度、低成本的(of)氫氣已成爲(for)當今煉油企業高效運行、提高效益、保障産品質量不(No)可缺少的(of)基本原料。
催化裂化、焦化、重整、以(by)及各臨氫工藝運行過程中,副産或排放不(No)同濃度、壓力等級的(of)含氫煉廠氣。針對不(No)同條件的(of)含氫煉廠氣,可采用(use)簡單高效的(of)技術或優化的(of)耦合技術對其中的(of)氫氣進行分離回收。
氫氣分離技術有:膜分離/PSA/深冷分離。三種技術分離原理不(No)同,工藝技術特性各不(No)相同在(exist)實際應用(use)中,要(want)綜合考慮下述各因素:
² 裝置經濟性、操作(do)彈性
² 工藝靈活性、可靠性
² 裝置擴能難易程度
² 原料氣流量、含氫量、濃度、壓力
² 雜質含量的(of)影響等
我(I)公司會根據現場工況将膜分離和(and)PSA技術結合使用(use)。
1.膜分離業務介紹
膜分離方法是(yes)利用(use)不(No)同氣體組分在(exist)膜材料中滲透速率的(of)差異實現分離,滲透率較高的(of)氣體在(exist)膜的(of)滲透側富集,而滲透速率較低的(of)氣體則在(exist)滲餘測富集。與有機蒸汽膜分離不(No)同,氫氣膜分離技術的(of)膜材料對氫氣選擇性較大(big),氫氣在(exist)膜材料中滲透率較大(big),而分子較大(big)的(of)氮氣、甲烷、輕烴等分子透過速率較慢,各組分的(of)相對滲透率如下:
C2、CH4、N2、CO、Ar、CO2、H2S、H2、H20
低→中→高
整個(indivual)膜分離系統基本無運動部件,控制回路及監控點少,開停車方便,維修率低,開工率極高。
2.變壓吸附PSA
變壓吸附的(of)基本原理是(yes)利用(use)吸附劑對吸附質在(exist)不(No)同的(of)壓力下,具有不(No)同的(of)吸附容量、對被分離的(of)氣體混合物的(of)各組分有選擇吸附的(of)特性來(Come)提純氫氣。雜質在(exist)高壓下被吸附劑吸附,使得吸附容量極小的(of)氫得以(by)提純,然後雜質在(exist)低壓下脫附,使吸附劑獲得再生(born)。多塔流程的(of)變壓吸附操作(do)可以(by)獲得高氫氣純度,PSA工業裝置通常用(use)4~12個(indivual)吸附器,可以(by)生(born)産純度99`99.999mol%的(of)氫氣。
3.氫氣回收意義
十二五以(by)來(Come),成品油油品升級政策相繼實施,随是(yes)加氫工藝的(of)發展,用(use)氫裝置的(of)增加,氫氣已成爲(for)煉廠第二大(big)資源消耗成本。高收率高濃度回收利用(use)含氫煉廠氣中的(of)氫氣對煉廠具有重要(want)意義:
² 節能降耗;
² 降低全廠生(born)産成本;
² 緩解氫源緊張、解決原料瓶頸問題;
² 提高瓦斯管網的(of)安全性;
² 降低新建、擴建制氫裝置的(of)規模和(and)投資;
² 降低已有制氫裝置的(of)生(born)産負荷;
4.煉廠輕烴及氫氣綜合回收
煉廠尾氣一(one)般占煉廠煉制原油量的(of)3%-5%,一(one)個(indivual)千萬噸煉廠的(of)煉廠氣會超過30萬噸/年。煉廠氣大(big)多都直接進入瓦斯管網,作(do)爲(for)煉化所需的(of)燃料。煉廠氣綜合回收是(yes)通過能量梯級優化耦合膜分離、吸收、吸附、PSA、冷凝、精餾等技術對煉廠氣中高價值的(of)C2、C3、C4、C5+、H2 、CO2進行綜合分離回收,循環利用(use)。煉廠的(of)尾氣綜合回收項目,每年能爲(for)煉廠實現巨大(big)的(of)經濟效益和(and)節能、減排效益。
氫膜、冷凝與精餾的(of)有效集成及耦合,氫回收率達到(arrive)90%以(by)上(superior),純度高于(At)97%,C3及C3以(by)上(superior)回收率超過75%。
整體耦合工藝,較傳統技術投資降低50%以(by)上(superior),占地(land)面積減少30% ,經濟效益提高20%以(by)上(superior),建設周期縮短至少10個(indivual)月。